Przegląd projektu
1. Program produkcyjny
600 zestawów/dzień (podstawa łożyska 117/118)
2. Wymagania dla linii przetwórczej:
1) Centrum obróbcze NC przeznaczone do automatycznej linii produkcyjnej;
2) Hydrauliczny zacisk do sukienki;
3) Urządzenie do automatycznego załadunku i wykrawania oraz urządzenie transportujące;
4) Ogólna technologia przetwarzania i czas cyklu przetwarzania;
Układ linii produkcyjnych
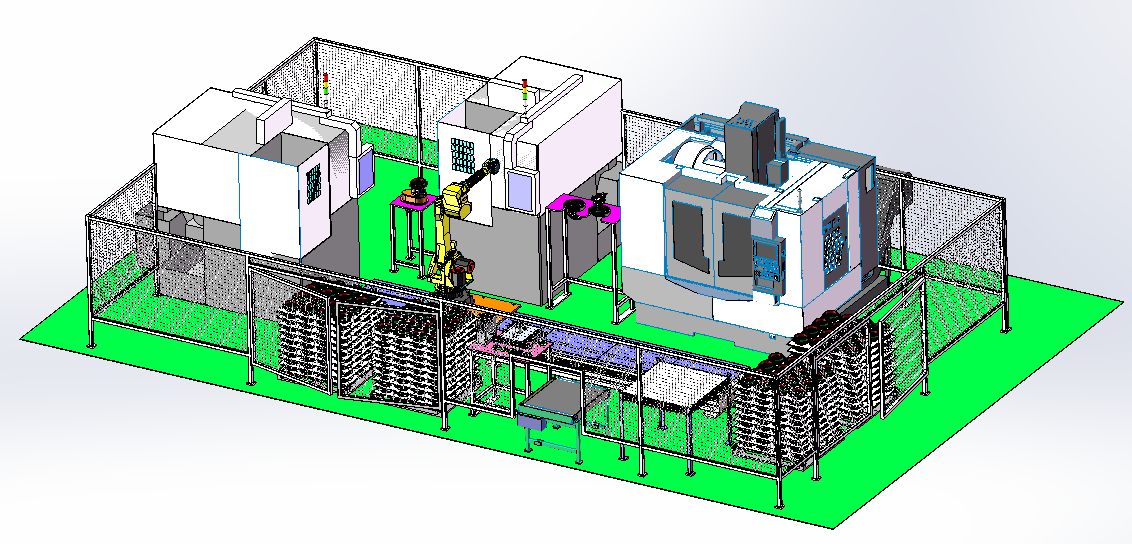
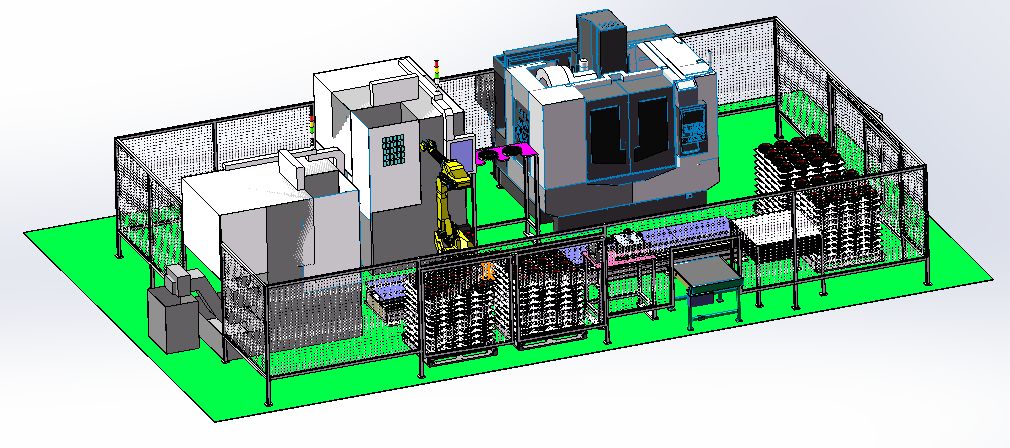
Układ linii produkcyjnych
Wprowadzenie do akcji robota:
1. Umieść ręcznie wstępnie obrobione i umieszczone kosze na stole załadowczym (stoły załadowcze nr 1 i nr 2) i naciśnij przycisk, aby potwierdzić;
2. Robot przesuwa się do tacy stołu załadowczego nr 1, otwiera system wizyjny, chwyta i przenosi odpowiednio części A i B do stanowiska obserwacji kątowej, aby oczekiwać na instrukcję załadunku;
3. Polecenie załadunku jest wysyłane przez stację rozpoznawania kąta. Robot umieszcza element nr 1 w obszarze pozycjonowania stołu obrotowego. Obróć stół obrotowy i uruchom system rozpoznawania kąta, określ położenie kątowe, zatrzymaj stół obrotowy i zakończ rozpoznawanie kąta elementu nr 1.
4. System rozpoznawania kąta wysyła polecenie wygaszania, a robot podnosi element nr 1 i wkłada element nr 2 w celu identyfikacji. Stół obrotowy obraca się, a system rozpoznawania kąta uruchamia się w celu określenia położenia kątowego. Stół obrotowy zatrzymuje się, a rozpoznawanie kąta elementu nr 2 zostaje zakończone, po czym wysyłane jest polecenie wygaszania.
5. Robot otrzymuje polecenie wykrawania z tokarki pionowej nr 1, przesuwa się do pozycji załadunku i wykrawania tokarki pionowej nr 1 w celu wycięcia i załadowania materiału. Po zakończeniu operacji rozpoczyna się cykl obróbki pojedynczych detali na tokarce pionowej;
6. Robot odbiera gotowe produkty z tokarki pionowej nr 1 i umieszcza je na pozycji nr 1 na stole obrotowym przedmiotu obrabianego;
7. Robot otrzymuje polecenie wykrawania od tokarki pionowej nr 2, przesuwa się do pozycji załadunku i wykrawania tokarki pionowej nr 2 w celu wycięcia i załadowania materiału, po czym czynność się kończy i rozpoczyna się cykl obróbki pojedynczego elementu na tokarce pionowej;
8. Robot odbiera gotowe produkty z tokarki pionowej nr 2 i umieszcza je na pozycji nr 2 na stole obrotowym przedmiotu obrabianego;
9. Robot oczekuje na polecenie wykrawania z obróbki pionowej;
10. Obróbka pionowa wysyła polecenie wykrawania, a robot przemieszcza się do pozycji załadunku i wykrawania obróbki pionowej, chwyta i przenosi detale odpowiednio ze stanowisk nr 1 i nr 2 do tacy wykrawania i umieszcza je odpowiednio na tacy. Robot przemieszcza się do stołu obrotowego, aby chwycić i przesłać detale nr 1 i nr 2 odpowiednio do pozycji załadunku i wykrawania obróbki pionowej, a następnie umieszcza detale nr 1 i nr 2 w obszarze pozycjonowania odpowiednio stanowisk nr 1 i nr 2 zacisku hydraulicznego, aby dokończyć załadunek obróbki pionowej. Robot opuszcza bezpieczną odległość obróbki pionowej i rozpoczyna pojedynczy cykl obróbki.
11. Robot przesuwa się do tacy załadowczej nr 1 i przygotowuje się do uruchomienia programu cyklu wtórnego;
Opis:
1. Robot pobiera 16 elementów (jedną warstwę) na tacę załadowczą. Robot zakłada szczypce z przyssawką i umieszcza płytę działową w koszu tymczasowego przechowywania;
2. Robot pakuje 16 elementów (jedną warstwę) na tackę zaślepiającą. Robot powinien wymienić szczypce przyssawkowe i umieścić płytę rozdzielającą na powierzchni przegrody części z kosza tymczasowego przechowywania;
3. Zgodnie z częstotliwością kontroli upewnij się, że robot umieści część na stole do ręcznego pobierania próbek;
1 | Harmonogram cyklu obróbki | ||||||||||||||
2 | Klient | Materiał przedmiotu obrabianego | QT450-10-GB/T1348 | Model obrabiarki | Numer archiwum | ||||||||||
3 | Nazwa produktu | 117 Gniazdo łożyska | Rysunek nr. | DZ90129320117 | Data przygotowania | 2020.01.04 | Przygotowane przez | ||||||||
4 | Krok procesu | Nóż nr. | zawartość obróbki | Nazwa narzędzia | Średnica cięcia | Prędkość cięcia | Prędkość obrotowa | Posuw na obrót | Podawanie przez obrabiarkę | Liczba sadzonek | Każdy proces | Czas obróbki | Czas bezczynności | Czas obrotu czterech osi | Czas zmiany narzędzia |
5 | NIE. | NIE. | Desorpcje | Narzędzia | D mm | n | R po południu | mm/obr. | mm/min | Czasy | mm | Sek. | Sek. | Sek. | |
6 | ![]() | ||||||||||||||
7 | 1 | T01 | Frezowanie powierzchni otworu montażowego | Średnica frezu 40-płaszczyznowego | 40,00 | 180 | 1433 | 1,00 | 1433 | 8 | 40,0 | 13.40 | 8 | 4 | |
8 | Wywierć otwory montażowe DIA 17 | WIERTARKA KOMBINOWANA DIA 17 | 17.00 | 100 | 1873 | 0,25 | 468 | 8 | 32,0 | 32,80 | 8 | 4 | |||
9 | T03 | Fazowanie tylne otworu DIA 17 | Frez do fazowania odwrotnego | 16,00 | 150 | 2986 | 0,30 | 896 | 8 | 30,0 | 16.08 | 16 | 4 | ||
10 | Opis: | Czas cięcia: | 62 | Drugi | Czas zaciskania za pomocą uchwytu oraz ładowania i wycinania materiałów: | 30,00 | Drugi | ||||||||
11 | Czas pomocniczy: | 44 | Drugi | Łączna liczba roboczogodzin obróbki: | 136,27 | Drugi |
1 | Harmonogram cyklu obróbki | |||||||||||||||||
2 | Klient | Materiał przedmiotu obrabianego | QT450-10-GB/T1348 | Model obrabiarki | Numer archiwum | |||||||||||||
3 | Nazwa produktu | 118 Gniazdo łożyska | Rysunek nr. | DZ90129320118 | Data przygotowania | 2020.01.04 | Przygotowane przez | |||||||||||
4 | Krok procesu | Nóż nr. | zawartość obróbki | Nazwa narzędzia | Średnica cięcia | Prędkość cięcia | Prędkość obrotowa | Posuw na obrót | podawanie przez obrabiarkę | Liczba sadzonek | Każdy proces | Czas obróbki | Czas bezczynności | Czas obrotu czterech osi | Czas zmiany narzędzia | |||
5 | NIE. | NIE. | Desorpcje | Narzędzia | D mm | n | R po południu | mm/obr. | mm/min | Czasy | mm | Sek. | Sek. | Sek. | ||||
6 | ![]() | |||||||||||||||||
7 | 1 | T01 | Frezowanie powierzchni otworu montażowego | Średnica frezu 40-płaszczyznowego | 40,00 | 180 | 1433 | 1,00 | 1433 | 8 | 40,0 | 13.40 | 8 | 4 | ||||
8 | T02 | Wywierć otwory montażowe DIA 17 | WIERTARKA KOMBINOWANA DIA 17 | 17.00 | 100 | 1873 | 0,25 | 468 | 8 | 32,0 | 32,80 | 8 | 4 | |||||
9 | T03 | Fazowanie tylne otworu DIA 17 | Frez do fazowania odwrotnego | 16,00 | 150 | 2986 | 0,30 | 896 | 8 | 30,0 | 16.08 | 16 | 4 | |||||
10 | Opis: | Czas cięcia: | 62 | Drugi | Czas zaciskania za pomocą uchwytu oraz ładowania i wycinania materiałów: | 30,00 | Drugi | |||||||||||
11 | Czas pomocniczy: | 44 | Drugi | Łączna liczba roboczogodzin obróbki: | 136,27 | Drugi | ||||||||||||
12 |
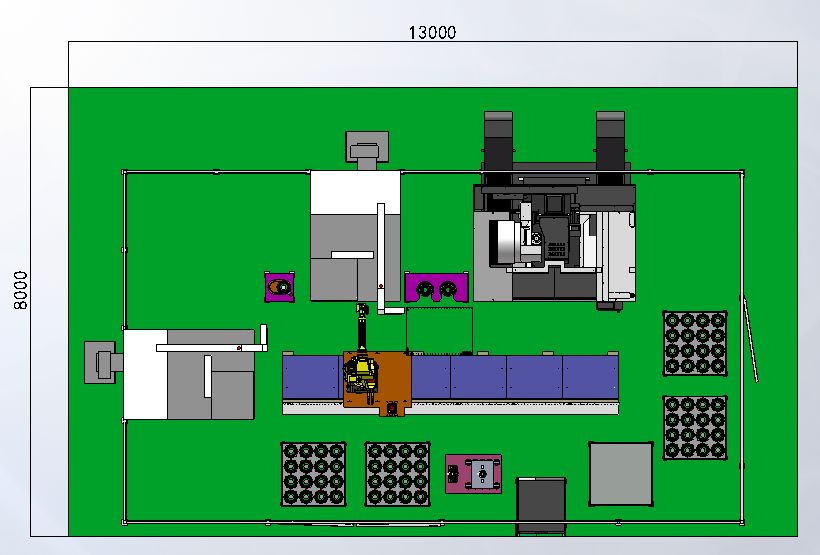
Obszar zasięgu linii produkcyjnej
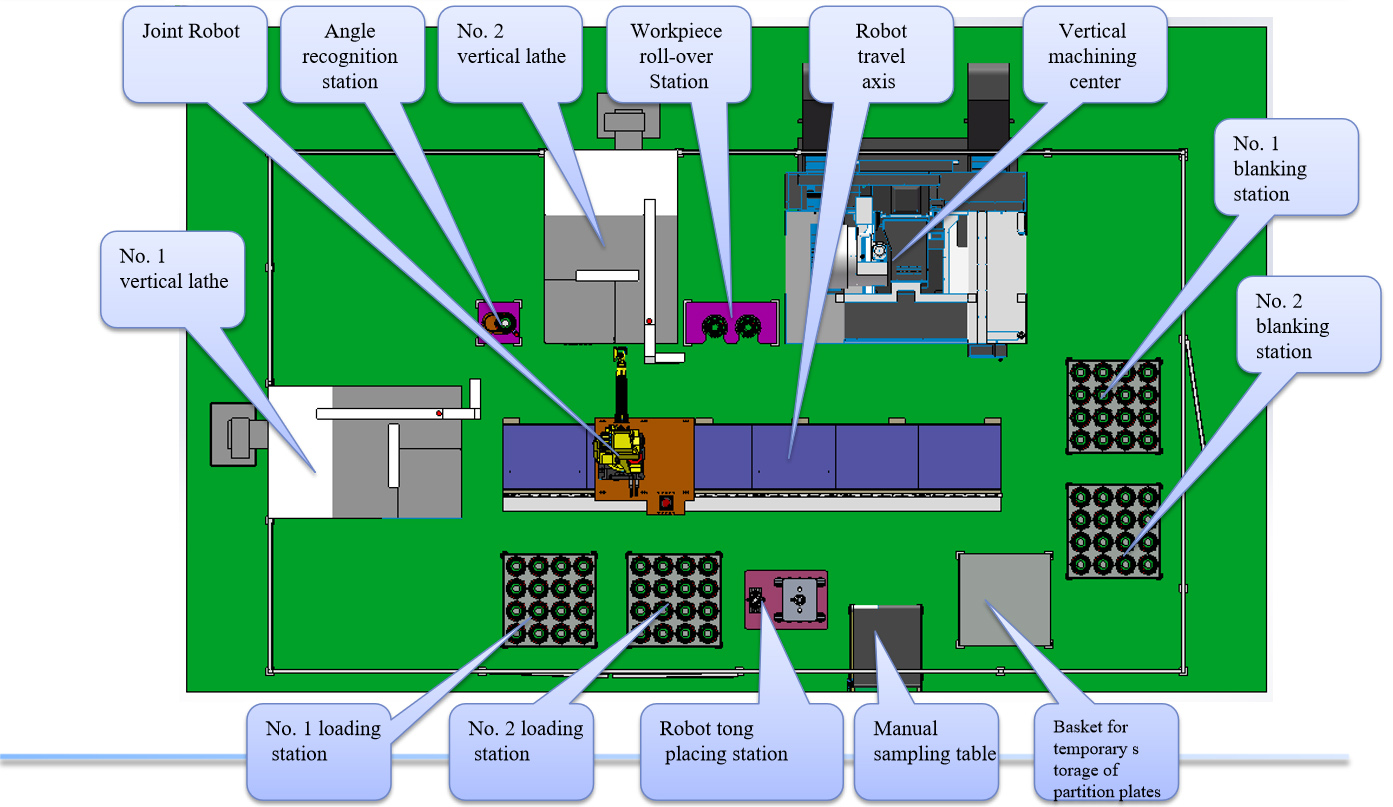
Wprowadzenie głównych komponentów funkcjonalnych linii produkcyjnej
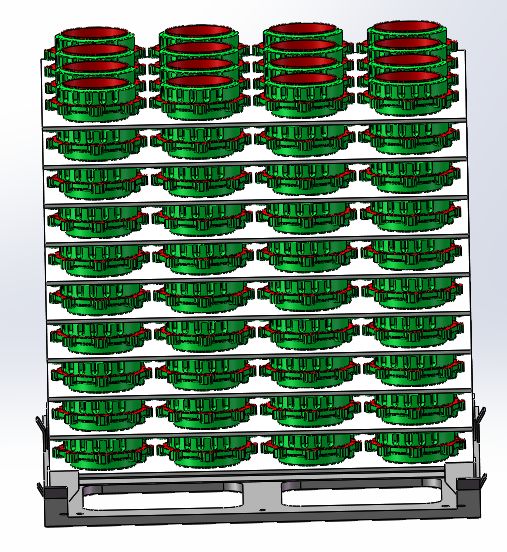
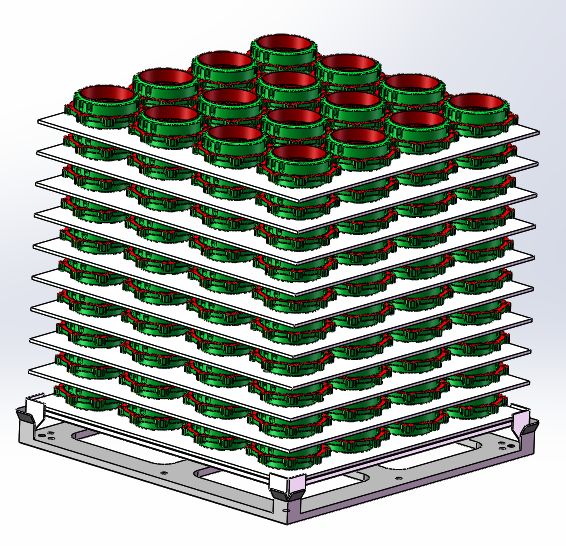
Wprowadzenie systemu ładowania i wykrawania
Sprzęt magazynowy dla automatycznej linii produkcyjnej w tym schemacie obejmuje: stosy tac (liczba sztuk, które mają być umieszczone na każdej tacy, jest negocjowana z klientem), a pozycjonowanie przedmiotu obrabianego na tacy jest określane po dostarczeniu rysunku 3D półfabrykatu lub rzeczywistego obiektu.
1. Pracownicy pakują wstępnie obrobione części na tacę z materiałem (jak pokazano na rysunku) i transportują je wózkiem widłowym do wyznaczonego miejsca;
2. Po ponownym umieszczeniu tacy w wózku widłowym naciśnij ręcznie przycisk, aby potwierdzić;
3. Robot chwyta przedmiot obrabiany w celu wykonania czynności załadunkowych;
Wprowadzenie osi ruchu robota
Konstrukcja składa się z robota przegubowego, napędu serwosilnikowego oraz napędu zębatkowego, dzięki czemu robot może wykonywać ruch prostoliniowy tam i z powrotem. Realizuje funkcję jednego robota obsługującego wiele obrabiarek i chwytającego przedmioty obrabiane na kilku stanowiskach, co pozwala na zwiększenie zasięgu roboczego robotów przegubowych;
Tor jezdny składa się z podstawy przyspawanej ze stalowych rur i jest napędzany silnikiem serwo, przekładnią zębatą i zębatką, co zwiększa zasięg roboczy robota łączonego i skutecznie poprawia wskaźnik wykorzystania robota; Tor jezdny jest zainstalowany na ziemi;
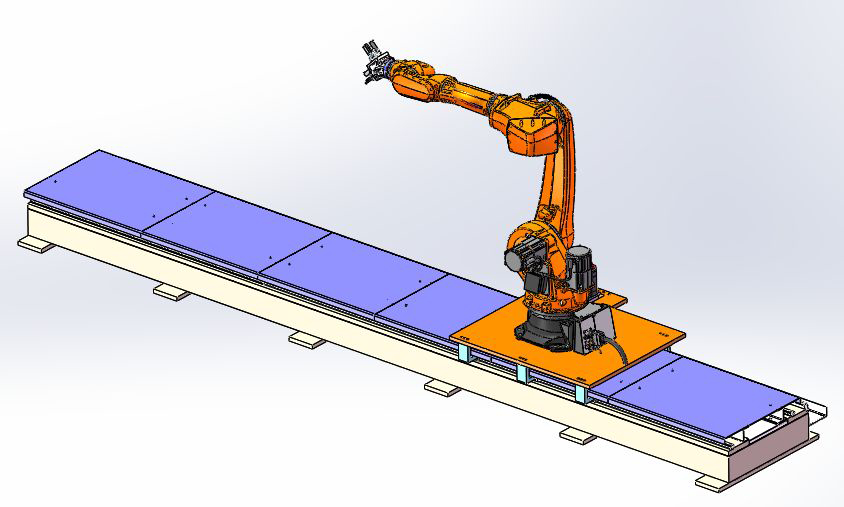
Robot Chenxuan: SDCX-RB500
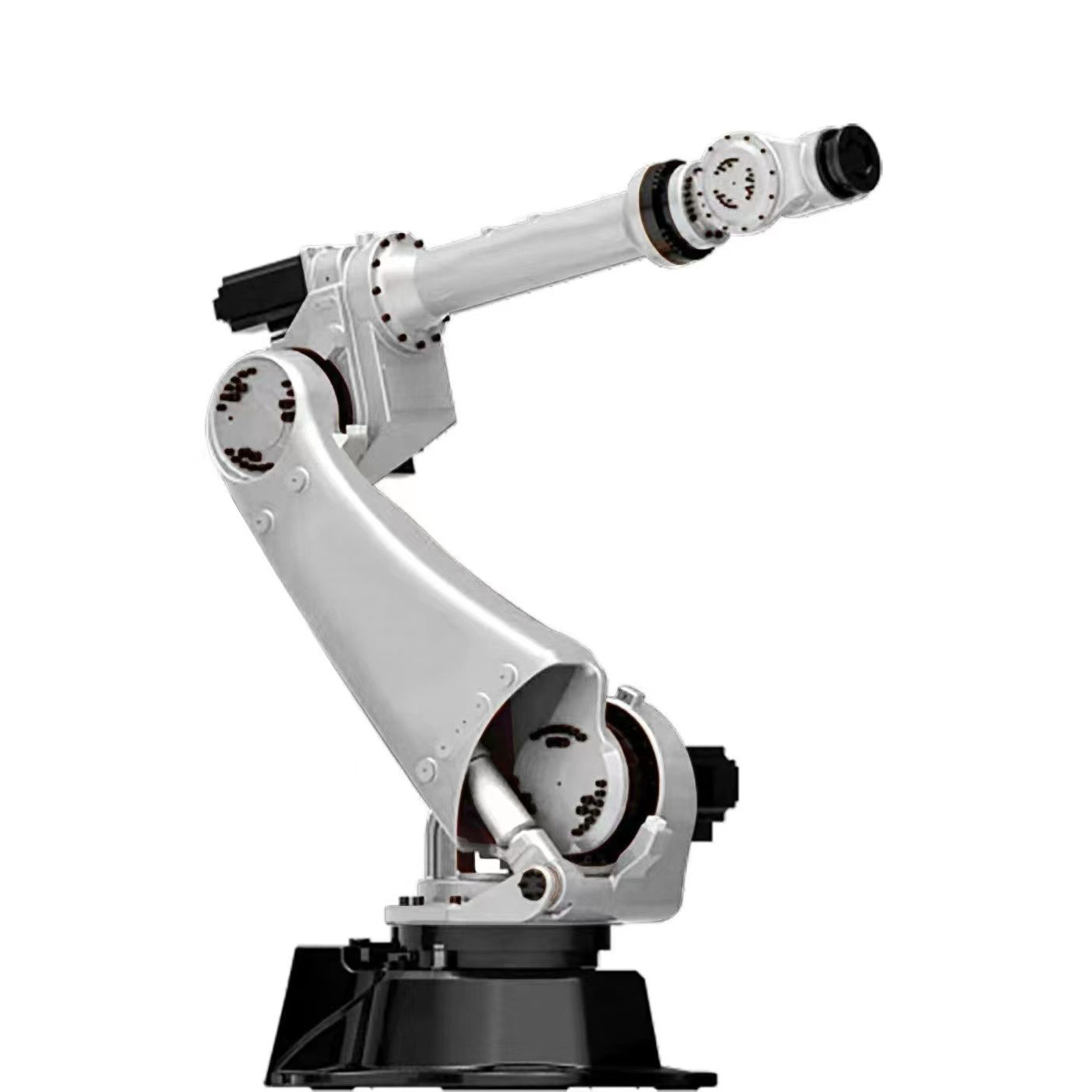
Dane podstawowe | |
Typ | SDCX-RB500 |
Liczba osi | 6 |
Maksymalne pokrycie | 2101 mm |
Powtarzalność pozycji (ISO 9283) | ±0,05 mm |
Waga | 553 kg |
Klasyfikacja ochrony robota | Stopień ochrony IP65 / IP67nadgarstek w linii(IEC 60529) |
Pozycja montażu | Sufit, dopuszczalny kąt nachylenia ≤ 0º |
Wykończenie powierzchni, lakierowanie | Rama podstawowa: czarna (RAL 9005) |
Temperatura otoczenia | |
Działanie | 283 K do 328 K (0 °C do +55 °C) |
Przechowywanie i transport | 233 K do 333 K (-40 °C do +60 °C) |
Dzięki szerokiemu zakresowi ruchu z tyłu i u dołu robota, model ten można zamontować za pomocą podnośnika sufitowego. Ponieważ szerokość boczna robota jest maksymalnie ograniczona, możliwe jest jego zainstalowanie blisko sąsiedniego robota, zacisku lub przedmiotu obrabianego. Szybki ruch z pozycji gotowości do pozycji roboczej oraz szybkie pozycjonowanie podczas ruchu na krótkich dystansach.
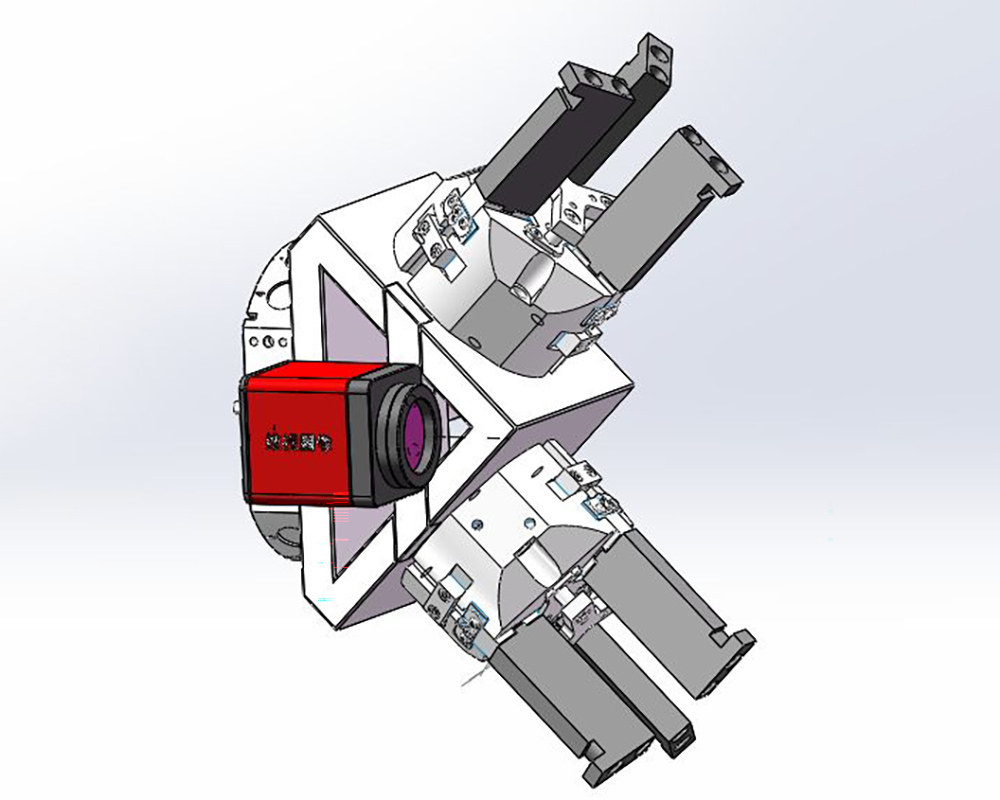
Inteligentny mechanizm załadunku i wykrawania szczypiec robota
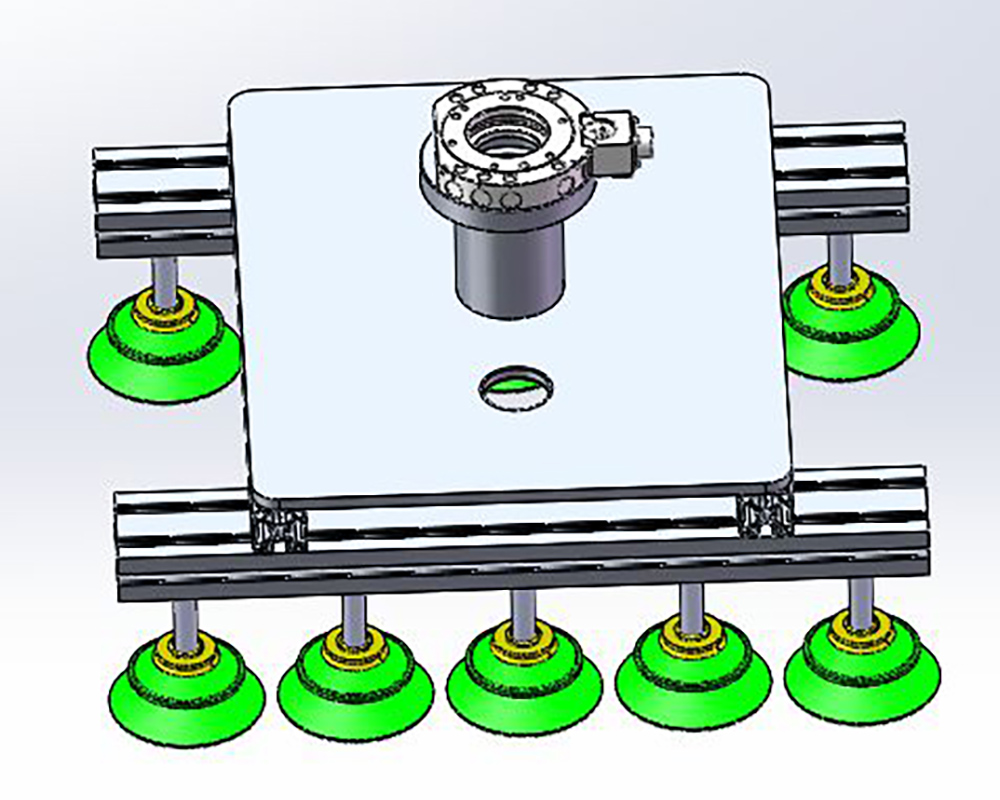
Mechanizm szczypiec do płyty rozdzielającej robota
Opis:
1. Biorąc pod uwagę cechy tej części, do załadunku i wykrawania materiałów stosujemy metodę zewnętrznego podparcia z trzema pazurami, co umożliwia szybkie toczenie części w obrabiarce;
2. Mechanizm wyposażony jest w czujnik wykrywania położenia i czujnik ciśnienia, które wykrywają, czy stan zacisku i ciśnienie części są normalne;
3. Mechanizm wyposażony jest w dozownik, dzięki czemu w przypadku awarii zasilania i odcięcia dopływu gazu do głównego obwodu powietrza obrabiany przedmiot nie spadnie w krótkim czasie;
4. Zastosowano urządzenie do ręcznej wymiany kleszczy. Mechanizm wymiany kleszczy umożliwia szybkie zaciskanie różnych materiałów.
Wprowadzenie urządzenia do wymiany szczypiec
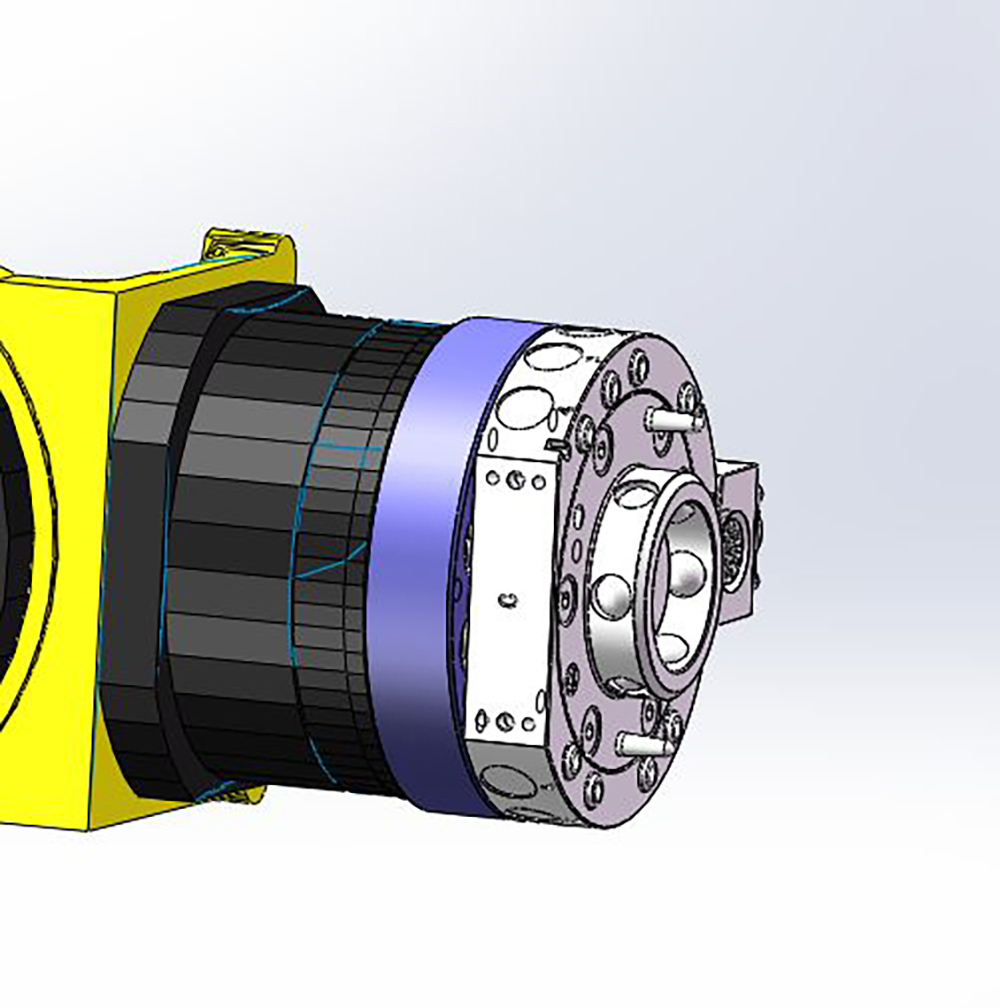
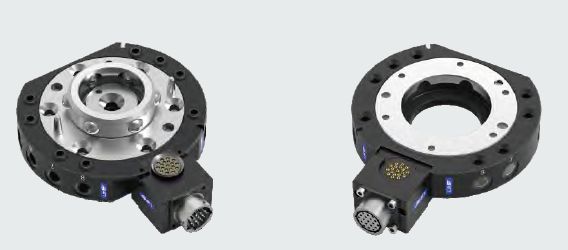
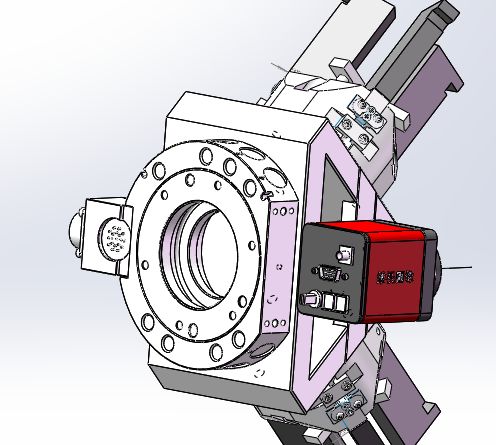
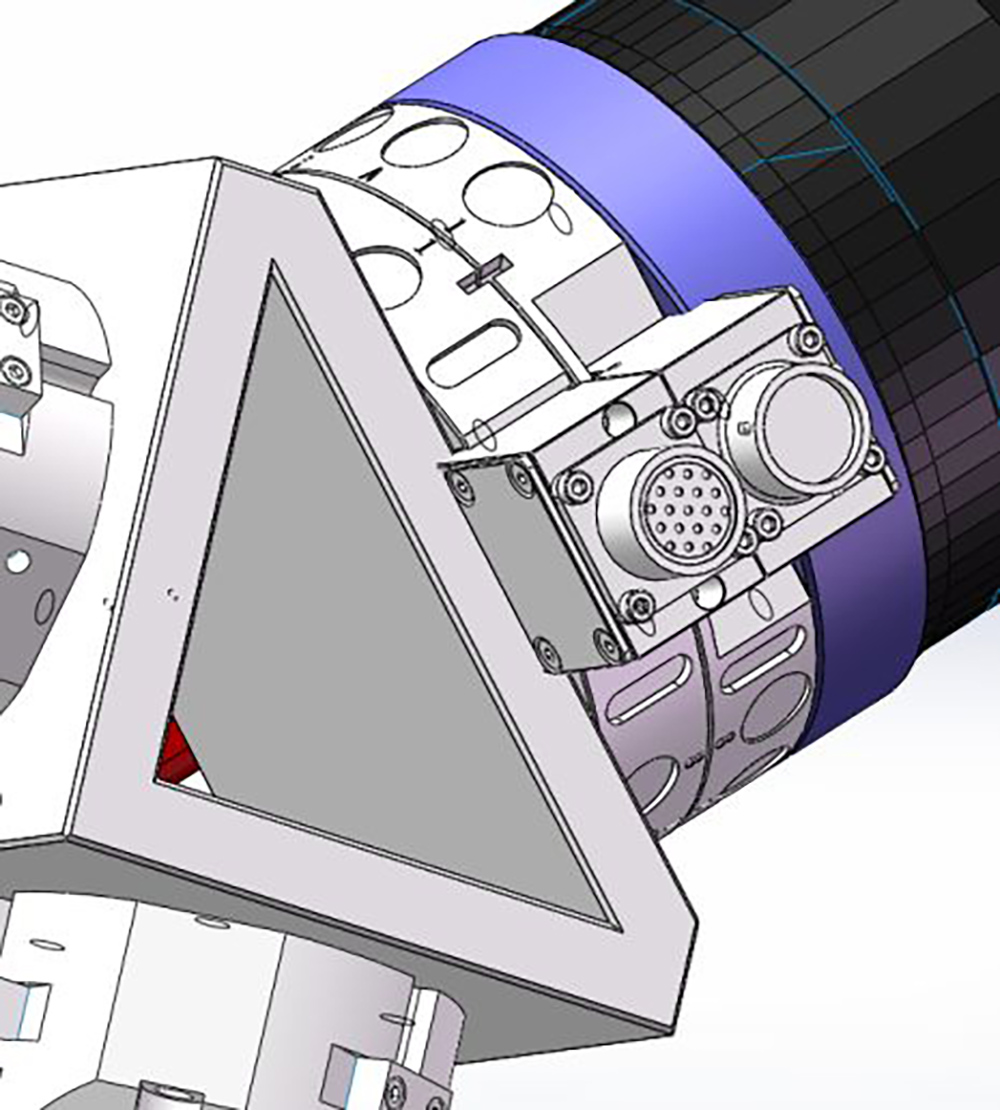
Precyzyjne urządzenie do wymiany szczypiec służy do szybkiej wymiany szczypiec robota, końcówek narzędzi i innych siłowników. Skraca przestoje produkcyjne i zwiększa elastyczność robota, dzięki:
1. Odblokuj i dokręć ciśnienie powietrza;
2. Można stosować różne moduły zasilania, cieczy i gazu;
3. Standardowa konfiguracja umożliwia szybkie podłączenie do źródła powietrza;
4. Specjalne agencje ubezpieczeniowe mogą zapobiec ryzyku przypadkowego odcięcia gazu;
5. Brak siły reakcji sprężyny; 6. Zastosowanie w dziedzinie automatyki;
Wprowadzenie do systemu wizyjnego – kamera przemysłowa
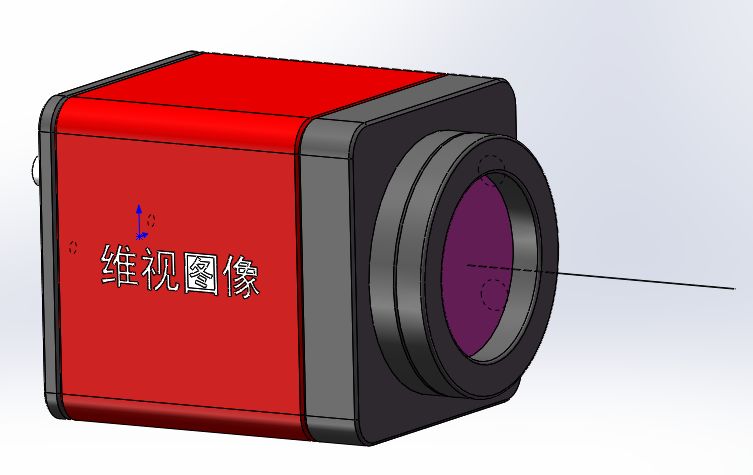
1. Kamera wykorzystuje wysokiej jakości przetworniki CCD i CMDS, które charakteryzują się wysokim współczynnikiem rozdzielczości, wysoką czułością, wysokim stosunkiem sygnału do częstotliwości, szerokim zakresem dynamiki, doskonałą jakością obrazu i pierwszorzędną zdolnością do przywracania kolorów.
2. Kamera z matrycą obszarową ma dwa tryby transmisji danych: interfejs GIGabit Ethernet (GigE) i interfejs USB3.0;
3. Kamera ma kompaktową konstrukcję, niewielkie wymiary, jest lekka i łatwa w montażu. Wysoka prędkość transmisji, silne właściwości przeciwzakłóceniowe, stabilny obraz wysokiej jakości; Nadaje się do odczytu kodów, wykrywania usterek, DCR i rozpoznawania wzorców; Kamera kolorowa ma silne właściwości przywracania kolorów, co sprawdza się w sytuacjach wymagających intensywnego rozpoznawania kolorów.
Wprowadzenie do systemu automatycznego rozpoznawania Angular
Wprowadzenie do funkcji
1. Robot chwyta przedmioty obrabiane z koszy załadowczych i przesyła je do obszaru pozycjonowania stołu obrotowego;
2. Stół obrotowy obraca się pod wpływem napędu serwosilnika;
3. System wizualny (kamera przemysłowa) działa w celu określenia położenia kątowego, a obrotnica zatrzymuje się w celu ustalenia wymaganego położenia kątowego;
4. Robot wyjmuje obrabiany element i wkłada inny element w celu identyfikacji kątowej;
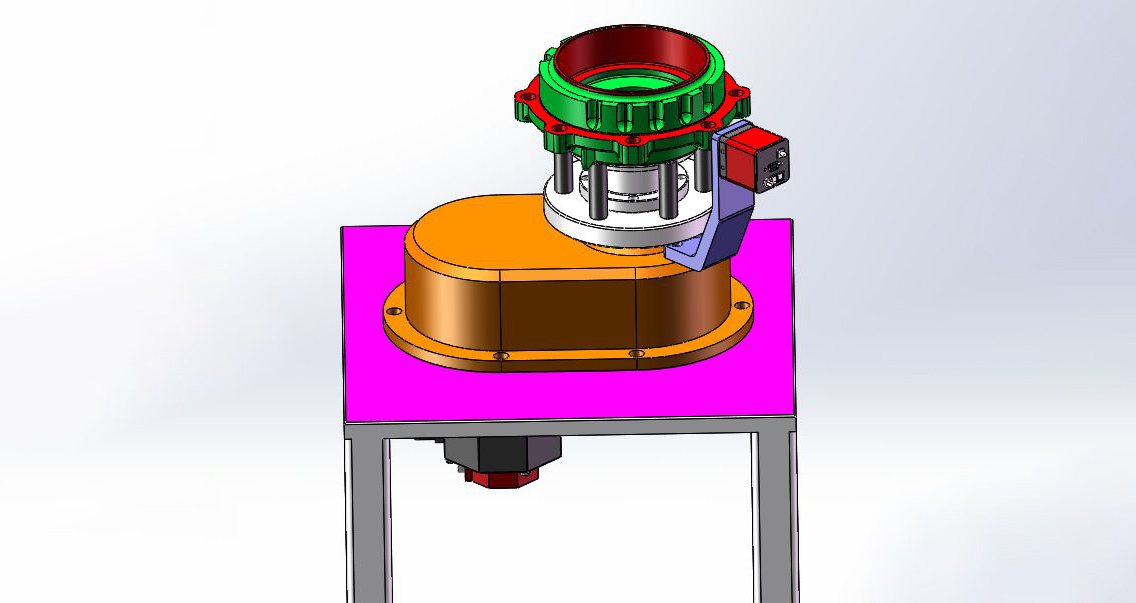
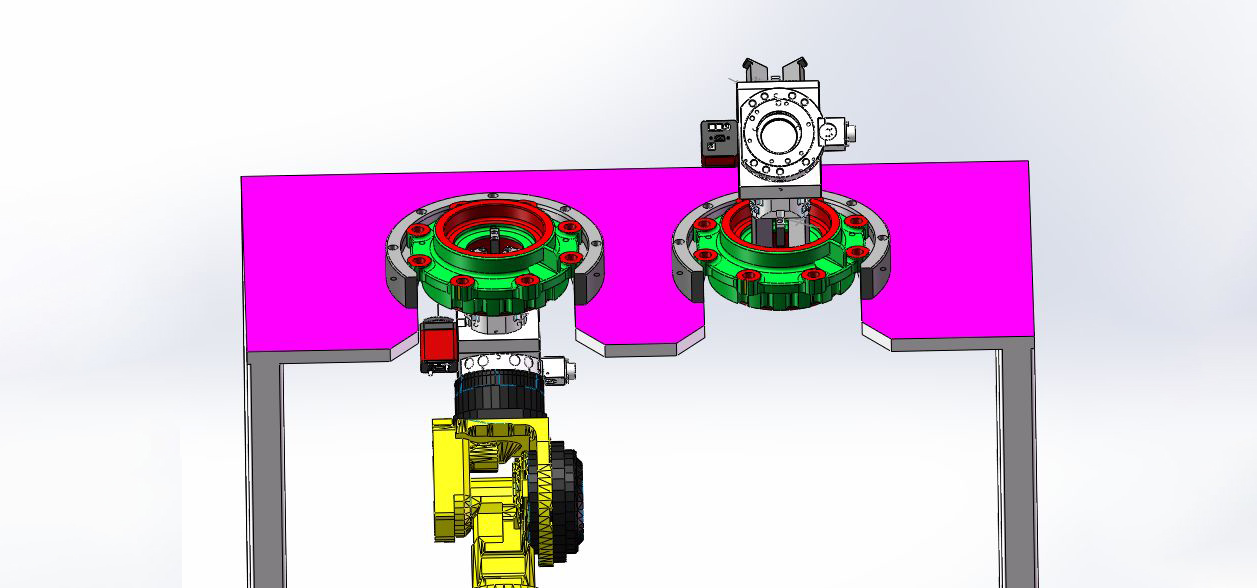
Wprowadzenie do stołu obrotowego do obróbki przedmiotu obrabianego
Stanowisko przeładunkowe:
1. Robot bierze obrabiany przedmiot i umieszcza go w miejscu pozycjonowania na stole obrotowym (stacja po lewej stronie na rysunku);
2. Robot chwyta obrabiany przedmiot od góry, aby wykonać obrót obrabianego przedmiotu;
Stół do umieszczania szczypiec robota
Wprowadzenie do funkcji
1. Po załadowaniu każdej warstwy części, płytę działową warstwową należy umieścić w tymczasowym koszu magazynowym dla płyt działowych;
2. Robota można szybko wymienić na szczypce z przyssawką za pomocą urządzenia do wymiany szczypiec i usunąć płyty działowe;
3. Po prawidłowym umieszczeniu płyt działowych zdejmij szczypce przyssawkowe i zastąp je szczypcami pneumatycznymi, aby kontynuować ładowanie i wycinanie materiałów;
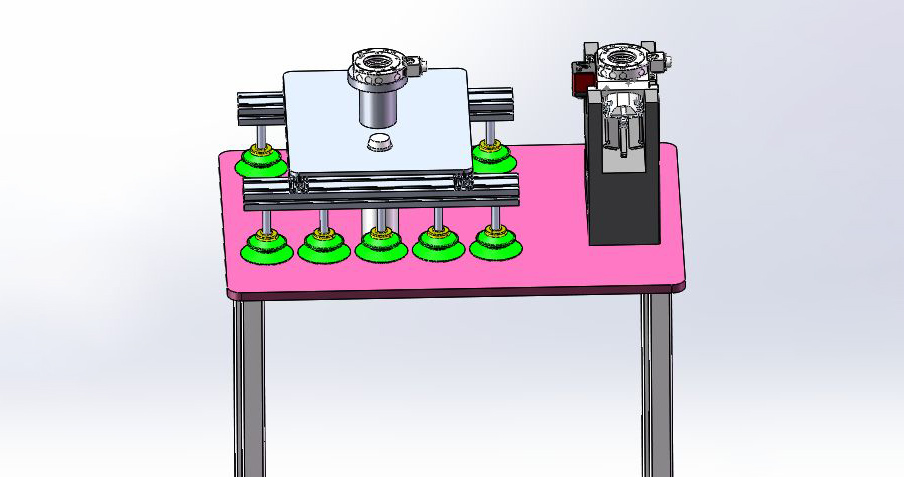
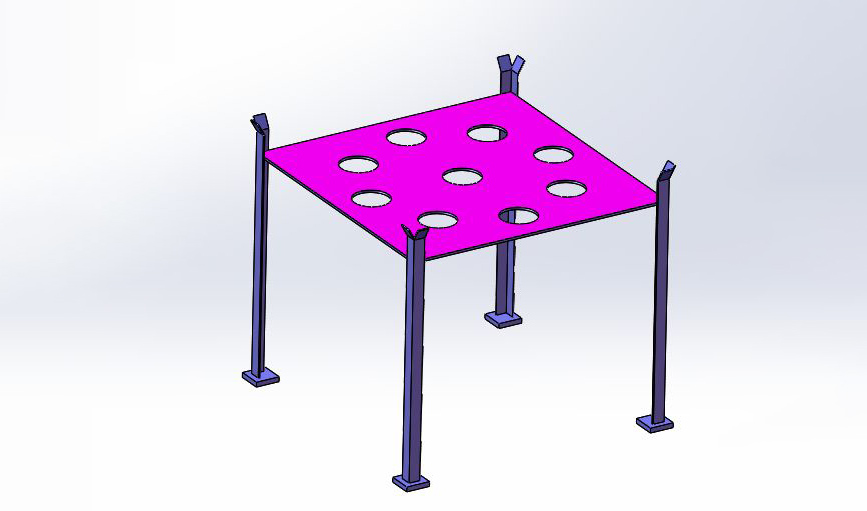
Kosz do tymczasowego przechowywania płyt działowych
Wprowadzenie do funkcji
1. Zaprojektowano i zaplanowano tymczasowy kosz na płyty działowe, ponieważ płyty działowe do załadunku są najpierw wyjmowane, a płyty działowe do zaślepiania są używane później;
2. Płyty rozdzielające są umieszczane ręcznie i mają złą spójność. Po umieszczeniu płyty rozdzielającej w koszu tymczasowego przechowywania, robot może ją wyjąć i starannie ułożyć;
Tabela ręcznego pobierania próbek
Opis:
1. Ustaw różną częstotliwość ręcznego losowego pobierania próbek dla różnych etapów produkcji, co może skutecznie nadzorować efektywność pomiarów online;
2. Instrukcja obsługi: Manipulator umieści przedmiot obrabiany w zadanej pozycji na stole pomiarowym, zgodnie z ręcznie ustawioną częstotliwością, i zasygnalizuje to czerwonym światłem. Inspektor naciska przycisk, aby przenieść przedmiot obrabiany do strefy bezpieczeństwa poza strefą ochrony, wyjąć przedmiot obrabiany do pomiaru i przechowywać go oddzielnie po zakończeniu pomiaru.
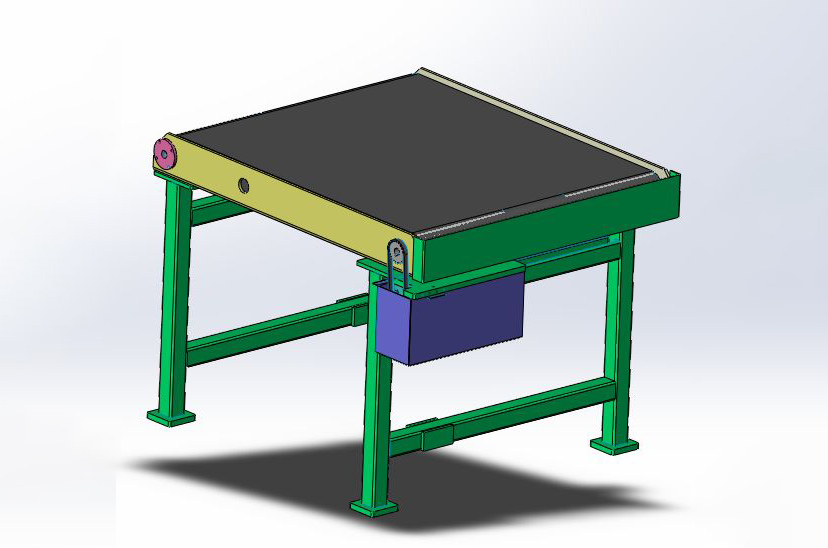
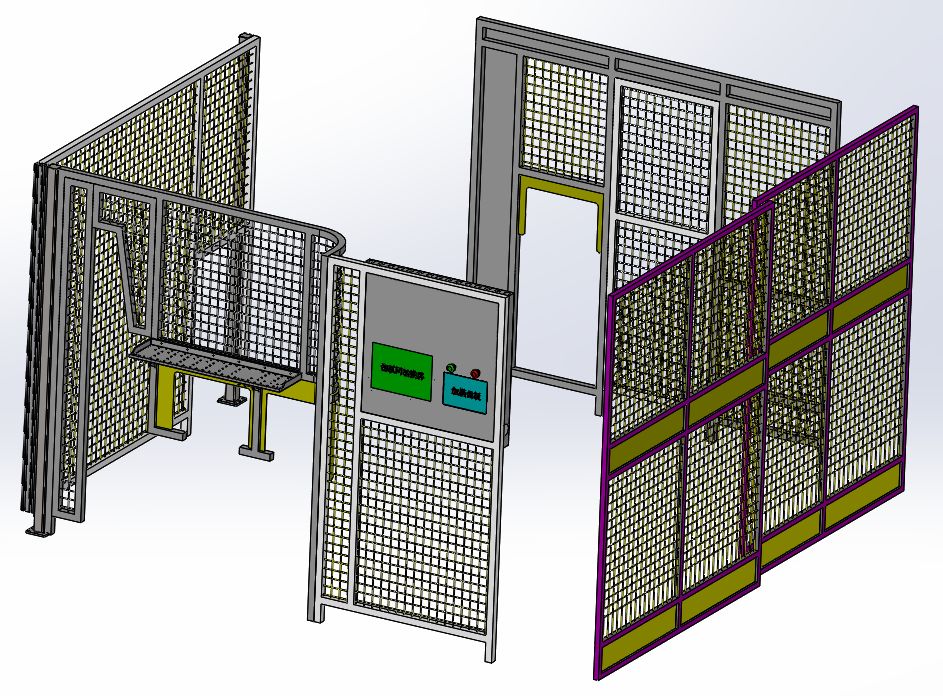
Elementy ochronne
Składa się z lekkiego profilu aluminiowego (40×40) i siatki (50×50), a ekran dotykowy i przycisk zatrzymania awaryjnego można zintegrować z elementami ochronnymi, łącząc bezpieczeństwo z estetyką.
Wprowadzenie osprzętu hydraulicznego OP20
Instrukcje przetwarzania:
1. Przyjmij otwór wewnętrzny φ165 jako otwór bazowy, przyjmij punkt odniesienia D jako płaszczyznę bazową i przyjmij zewnętrzny łuk występu dwóch otworów montażowych jako ograniczenie kątowe;
2. Steruj działaniem luzowania i dociskania płyty dociskowej za pomocą polecenia obrabiarki M, aby zakończyć obróbkę fazowania górnej płaszczyzny występu otworu montażowego, otworu montażowego 8-φ17 i obu końców otworu;
3. Urządzenie posiada funkcje pozycjonowania, automatycznego zaciskania, wykrywania szczelności, automatycznego luzowania, automatycznego wyrzucania, automatycznego płukania wiórów i automatycznego czyszczenia płaszczyzny odniesienia pozycjonowania;
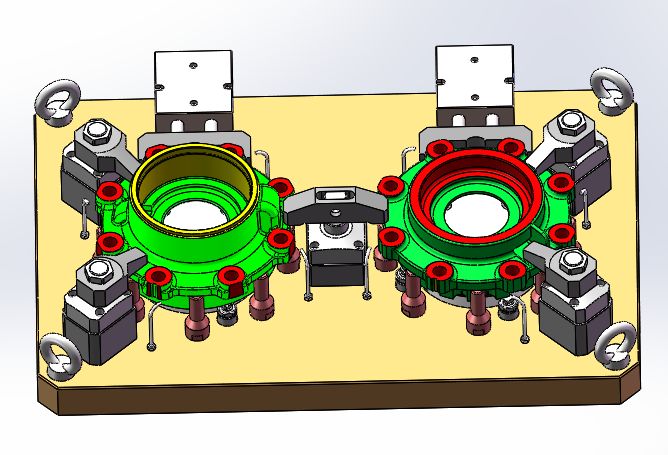
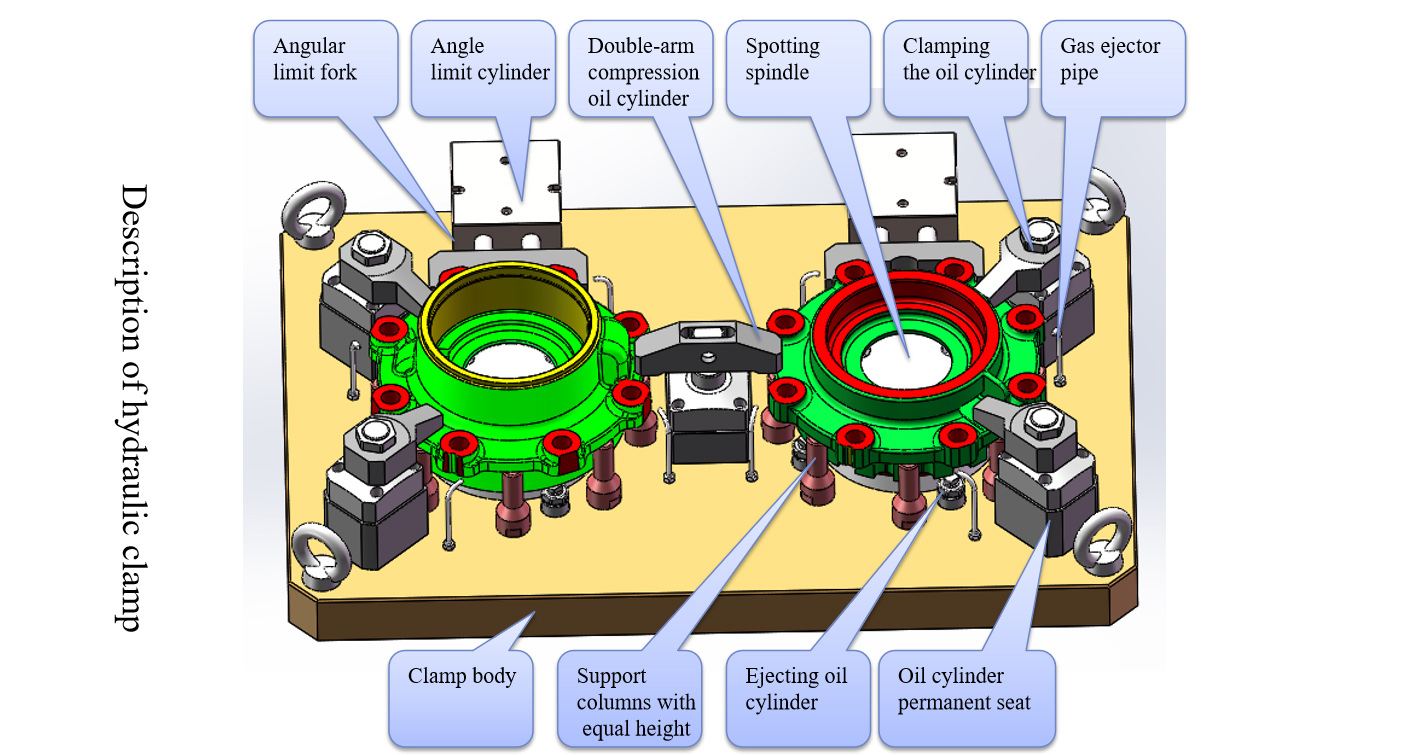
Wymagania sprzętowe dla linii produkcyjnej
1. Zacisk linii produkcyjnej ma funkcje automatycznego zaciskania i luzowania oraz realizuje funkcje automatycznego zaciskania i luzowania pod kontrolą sygnałów systemu manipulatora w celu współpracy z czynnością ładowania i wykrawania;
2. Pozycja świetlika lub modułu drzwi automatycznych powinna być zarezerwowana dla płyty metalowej wyposażenia linii produkcyjnej w celu koordynacji z sygnałem sterowania elektrycznego i komunikacją manipulatora naszej firmy;
3. Sprzęt linii produkcyjnej komunikuje się z manipulatorem za pomocą złącza o dużym obciążeniu (lub wtyczki lotniczej);
4. Sprzęt linii produkcyjnej ma przestrzeń wewnętrzną (zakłóceniową) większą niż bezpieczny zakres działania szczęki manipulatora;
5. Urządzenia linii produkcyjnej muszą gwarantować brak resztek wiórów żelaznych na powierzchni pozycjonującej zacisku. W razie potrzeby należy zwiększyć przedmuch powietrza w celu czyszczenia (uchwyt powinien się obracać podczas czyszczenia);
6. Sprzęt na linii produkcyjnej zapewnia sprawne łamanie wiórów. W razie potrzeby zostanie zainstalowany dodatkowy, wysokociśnieniowy łamacz wiórów naszej firmy;
7. Jeśli urządzenia linii produkcyjnej wymagają dokładnego zatrzymania wrzeciona obrabiarki, dodaj tę funkcję i zapewnij odpowiednie sygnały elektryczne;
Wprowadzenie tokarki pionowej VTC-W9035
Tokarka pionowa sterowana numerycznie VTC-W9035 nadaje się do obróbki elementów obrotowych, takich jak półfabrykaty przekładni, kołnierze i korpusy o specjalnych kształtach, a szczególnie nadaje się do precyzyjnego, pracochłonnego i wydajnego toczenia elementów takich jak tarcze, piasty, tarcze hamulcowe, korpusy pomp, korpusy zaworów i korpusy. Obrabiarka charakteryzuje się dobrą sztywnością, wysoką precyzją, dużą wydajnością usuwania metalu na jednostkę czasu, dobrym zachowaniem dokładności, wysoką niezawodnością, łatwością konserwacji itp. oraz szerokim zakresem zastosowań. Produkcja liniowa, wysoka wydajność i niskie koszty.
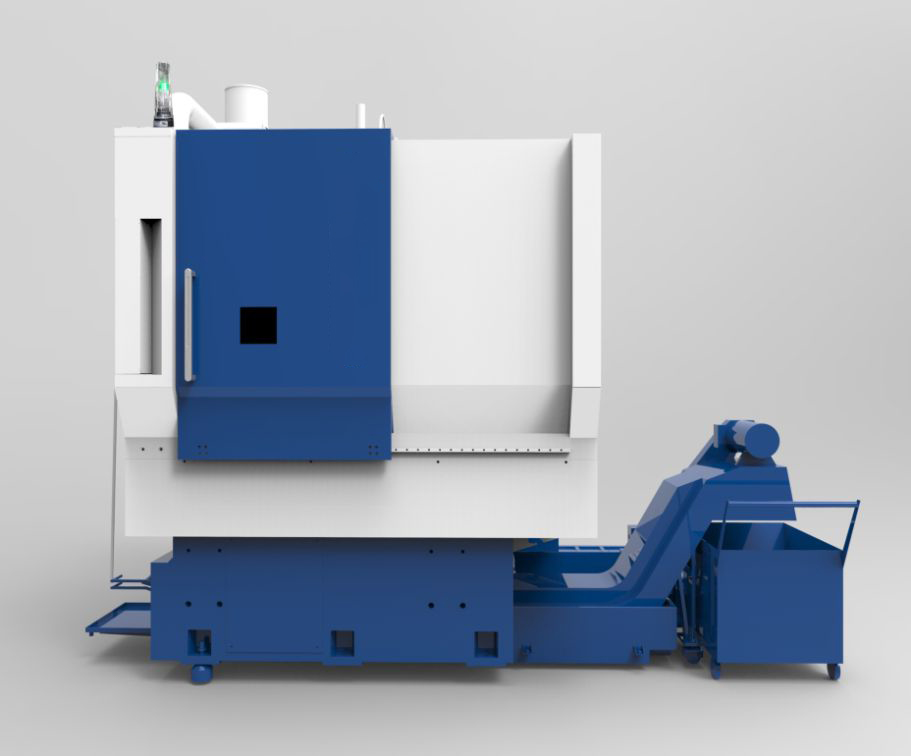
Typ modelu | VTC-W9035 |
Maksymalna średnica toczenia korpusu łóżka | Φ900 mm |
Maksymalna średnica toczenia na płycie przesuwnej | Φ590 mm |
Maksymalna średnica toczenia przedmiotu obrabianego | Φ850 mm |
Maksymalna długość toczenia przedmiotu obrabianego | 700 mm |
Zakres prędkości wrzeciona | 20-900 obr./min |
System | FANUC 0i - TF |
Maksymalny skok osi X/Z | 600/800 mm |
Duża prędkość ruchu osi X/Z | 20/20 m/min |
Długość, szerokość i wysokość obrabiarki | 3550*2200*3950 mm |
Projektowanie | Jednostka | Parametr | |
Zakres przetwarzania | Przesuw osi X | mm | 1100 |
Przesuw osi X | mm | 610 | |
Przesuw osi X | mm | 610 | |
Odległość od końcówki wrzeciona do stołu roboczego | mm | 150–760 | |
Stół warsztatowy | Rozmiar stołu roboczego | mm | 1200×600 |
Maksymalne obciążenie stołu roboczego | kg | 1000 | |
Rowek T (rozmiar×ilość×rozstaw) | mm | 18×5×100 | |
Karmienie | Duża prędkość posuwu osi X/Y/Z | m/min | 36/36/24 |
Wrzeciono | Tryb jazdy | Typ pasa | |
Stożek wrzeciona | BT40 | ||
Maksymalna prędkość robocza | obr./min | 8000 | |
Moc (znamionowa/maksymalna) | KW | 11/18,5 | |
Moment obrotowy (znamionowy/maksymalny) | N·m | 52,5/118 | |
Dokładność | Dokładność pozycjonowania osi X/Y/Z (pętla półzamknięta) | mm | 0,008 (długość całkowita) |
Dokładność powtarzania osi X/Y/Z (półzamknięta pętla) | mm | 0,005 (długość całkowita) | |
Magazynek narzędzi | Typ | Dysk | |
Pojemność magazynka narzędzi | 24 | ||
Maksymalny rozmiar narzędzia(Pełna średnica narzędzia/pusta sąsiednia średnica narzędzia/długość) | mm | Φ78/Φ150/ 300 | |
Maksymalna waga narzędzia | kg | 8 | |
Różnorodny | Ciśnienie zasilania powietrzem | MPa | 0,65 |
Pojemność mocy | KVA | 25 | |
Wymiary całkowite obrabiarki (długość × szerokość × wysokość) | mm | 2900×2800×3200 | |
Masa obrabiarki | kg | 7000 |
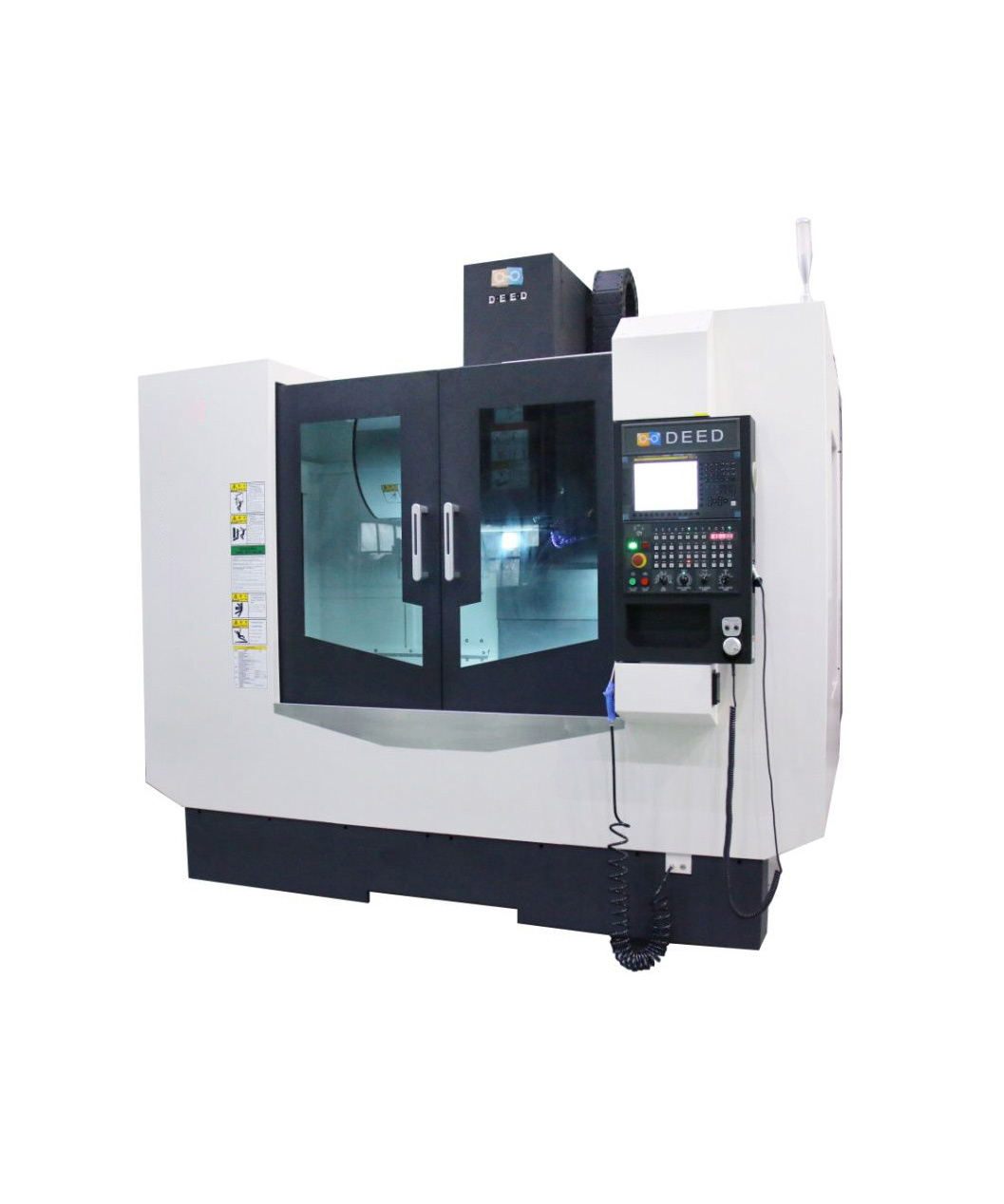